

This project focused on a challenging task of recovering low-temperature latent heat that can have a paradigm shift in the way thermal process units will be designed and operated to achieve high-energy efficiency and significantly reduce the carbon footprint as well as water footprint. Publication Date: Fri Aug 01 00:00: Research Org.: Argonne National Lab., IL (USA) OSTI Identifier: 7013430 Report Number(s): ANL/CNSV-9 DOE Contract Number: W-31-109-ENG-38 Resource Type: Technical Report Country of Publication: United States Language: English Subject: 32 ENERGY CONSERVATION, CONSUMPTION, AND UTILIZATION ALKENES ENERGY DEMAND PRODUCTION PETROCHEMICAL PLANTS ENERGY ANALYSIS HEAT RECOVERY MATERIAL BALANCE BUTADIENE CONSUMPTION RATES DATA COMPILATION ETHYLENE MATERIAL SUBSTITUTION NATURAL GAS PETROCHEMICALS PETROLEUM PLASTICS POLYESTERS PROCESS HEAT PROPYLENE RECYCLING RUBBERS CHEMICAL PLANTS DATA DEMAND DIENES ELASTOMERS ENERGY ENERGY RECOVERY ENERGY SOURCES ESTERS FLUIDS FOSSIL FUELS FUEL GAS FUELS GAS FUELS GASES HEAT HYDROCARBONS INDUSTRIAL PLANTS INFORMATION NUMERICAL DATA ORGANIC COMPOUNDS ORGANIC POLYMERS PETROLEUM PRODUCTS POLYENES POLYMERS RECOVERY 320300* - Energy Conservation, Consumption, & Utilization- Industrial & Agricultural = ,Įvaporation and crystallization are key thermal separation processes for concentrating and purifying inorganic and organic products with energy consumption over 1,000 trillion Btu/yr.
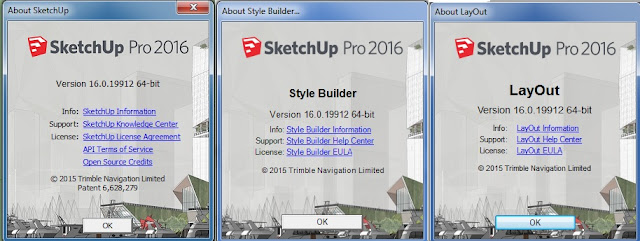
This steam accounts for a major fraction of the industry's energy input. Further investigation of the following areas could yield both material and energy savings in the olefins industry: (1) recycling of petrochemical products to recover energy in addition to that recoverable through combustion, (2) impact of more » feedstock substitution on utilization of available national resources, and (3) effective use of the heat embodied in process steam. The energy foregone in plastics production ranges from 12,100 Btu/lb for the new linear low-density polyethylene to 77,200 Btu/lb for nylon 66, which is about 60% of the total energy input for that product. The energy foregone in the production of ethylene is estimated to be 7800 Btu/lb. Petrochemical processes use fuels as feedstocks, as well as for process energy, and a portion of this energy is not foregone and can be recovered through combustion of the products. (About 1.4 Q is used to produce plastic derivatives of olefins). For example, recycling of a single plastic product, polyester soft drink bottles, could have recovered about 0.014 Q in 1979. Substantial amounts of this energy could be recovered through recycling. It is estimated that their production requires an input energy of 2 Q, which is 50% of the energy used in the production of all petrochemicals. Production of olefins and their derivatives uses almost 3.5% of the oil and gas consumed annually in the United States.
